焼結金属材の平面研削・研磨(ラップ)・内径外径・ねじ研削加工はお任せください!
大古精機では精密ゲージ設計製作の加工技術・検査能力を活かして、精密研削加工を行なっております。
大古精機では、これまでの実績をもとに独自に加工条件を設定し、試作を行なっておりますので、焼結金属材の平面研削加工、研磨(ラップ)加工、内径外径加工、ねじ研削加工につきましても是非ご相談ください。
大古精機の精密研磨加工の詳細については、こちらをご覧ください。
焼結金属材について
焼結金属材は、金属粉末を圧縮成形し、その後、高温で焼結(焼き固める)して製造される材料です。このプロセスを焼結プロセスと呼びます。粉末冶金(パウダーメタル)技術の一環として用いられ、複雑な形状や高精度の部品を効率よく製造する手段として広く利用されています。
製造プロセス
- 粉末調製: 金属粉末を適切な粒度に調整します。一般に、アトマイズ法(液体金属を霧状にする方法)や機械的粉砕法が使用されます。
- 混合: 必要に応じて、異なる金属粉末や添加剤(例えば、潤滑剤)を均一に混合します。
- 成形: 金属粉末をダイや型に入れ、高圧で圧縮して所望の形状に成形します。このプロセスをプレス成形と呼びます。
- 脱脂: 成形体から潤滑剤や有機物を除去するためのプロセスです。一般に、低温での熱処理や溶媒洗浄が行われます。
- 焼結: 成形体を高温(通常800~1300℃)で加熱し、粉末粒子間を結合させて固体化します。このプロセスによって、最終的な強度と形状が得られます。
- 後加工: 必要に応じて、機械加工、熱処理、表面処理などの後加工が行われます。
特徴と利点
- 高い形状自由度: 複雑な形状の部品を一度の成形で製造できるため、後加工が少なくて済みます。
- 高精度: 微細な寸法公差を維持できるため、高精度な部品の製造が可能です。
- 材料の有効利用: 材料のロスが少なく、リサイクル性にも優れています。
- 高い強度と耐久性: 焼結によって粒子間が強固に結合されるため、高い強度と耐久性が得られます。
- コスト効率: 大量生産に適しており、コスト効率が高いです。
用途
焼結金属材は、さまざまな産業で広く利用されています。具体的な用途には以下のようなものがあります。
- 自動車産業: 歯車、軸受、バルブシートなどのエンジン部品やトランスミッション部品。
- 電機・電子産業: 磁性体部品、接点材、フィルター。
- 医療機器: 人工関節、歯科用インプラント。
- 一般機械: 切削工具、耐摩耗部品。
焼結プロセスの課題
- 高コストの設備投資: 高精度な成形や焼結には専用の設備が必要であり、初期投資が高額です。
- 材料の制約: 使用できる材料が限定されている場合があります。
- 品質管理の難しさ: 微細な粉末を扱うため、品質管理が難しく、高度な技術が求められます。
焼結金属の進化と展望
技術の進化により、より高性能な焼結金属材の開発が進んでいます。ナノ粉末の利用や複合材料の開発、新しい成形・焼結技術の導入により、従来の焼結金属材の性能を超える新しい材料が誕生しています。これにより、さらに広範な応用が期待されています。
このように、焼結金属材はその多様な特性と利点から、さまざまな産業で重要な役割を果たしています。
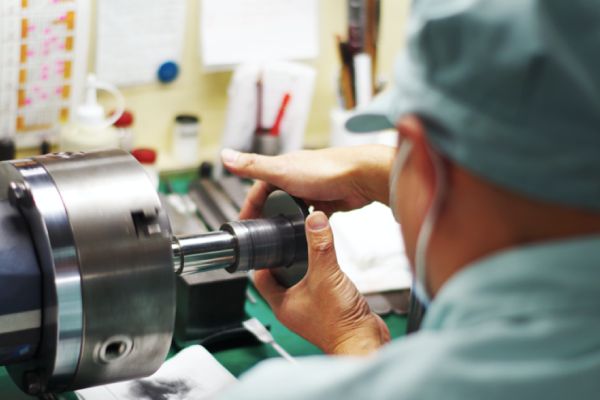
精密研磨加工・ラップ加工
大古精機の精密加工/測定技術を活かし、精密研磨加工、ラップ加工を請け負います。